Our activities focus on property development, residential building, non-residential building and infrastructure, and in these areas we aim to develop propositions that are a close match with the needs of society, clients and end-users. This is why we closely monitor all the trends and developments in society. For instance, the government wants 'health' to be explicitly included in the development of any spatial policies. This mindset is laid down in the likes of the National Policy Document on Health 2020-2024. Local authorities are being told to put users first and encourage a healthy lifestyle. Heijmans embraces this thinking, as creating a healthy living environment has been our mission for many years. This is why we always try to improve biodiversity, both in the construction of residential areas (for instance, Maanwijk in Leusden), roads (the Eemnes/Utrecht stretch of the A27 motorway) and landscaping projects (for instance, the National Military Museum in Soesterberg). Our ambition is to leave every area we work in better than we found it.
Our second focus is on safety in the construction and infrastructure sector. Unfortunately, there are still too many accidents every year, which is why we want to work with the industry as a whole to change that. We joined forces with a number of leading construction companies and clients in construction, infra and installation engineering, to draw up the Governance Code for Safety in Construction (GCVB). This lays down shared principles and core values in the areas of standardisation, chain cooperation, training and knowledge sharing. Together with other players in the sector (including Bouwend Nederland and SSVV), we are also working on a sector-wide learning platform for individual employees, integrating the Uniform Reporting App (UMA), which enables employees to report unsafe situations at building sites. Below, we outline some other significant social trends we have identified and how we are responding to them.
Pressure on the labour market
The labour market is tight, so we are pleased that we have managed to retain many employees and also gain new colleagues in recent years. These include both highly educated people and young people trained in practical technical disciplines. However, the tightness of the labour market does remain a concern for the future. Many parents encourage their children to study, so not enough people are trained in practical disciplines. Heijmans is committed at many levels to stimulating interest in engineering, construction and manufacturing technology. For example, several of our colleagues act as guest lecturers at various levels, we organise an annual minor study for students from Avans University of Applied Sciences, as well as a challenge for pupils from various schools of technology, and we help to organise company days. We also have a large number of trainees, interns and apprentices in our organisation.
Climate change
The impact of climate change was once again clearly visible last year. We saw a long period of drought and heat stress (higher temperatures in densely built-up cities). At the same time, we faced increasingly heavy rainfall that led to flooding. The need for climate-adaptive building and innovation is becoming increasingly urgent. The Paris climate goals set the framework for this. We need to provide more greenery, space for water and biodiversity. This is something we have been doing in our area developments for many years, and we measure the impact we have using NL Greenlabel. The projects that are now being delivered are future-proof, and even in ongoing projects we are always on the lookout for opportunities to improve and make them even more sustainable.
High Water Protection Programme
As part of the Delta Plan for Water Safety, over the next 30 years the High Water Protection Programme (HWBP) will work to strengthen 1,500 kilometres of dykes and five hundred locks and pumping stations. The aim of the programme is to make sure all primary flood defences are up to standard by 2050. Sustainability, circularity, knowledge development and innovation are important aspects in all HWBP projects. Heijmans is carrying out several of these projects, including those at Gorinchem-Waardenburg and Lauwersmeerdijk.
Gorinchem – Waardenburg dyke reinforcement
The Rivierenland water board has commissioned the Graaf Reinald combine to restore a 23-kilometre stretch of the dyke between Gorinchem and Waardenburg to its former glory. This project is part of the government’s High Water Protection Programme and has to ensure that the dyke section will once again meet safety standards in 2026. Heijmans is working in this alliance with GMB and de Vries & van de Wiel, partners in the Emission-free Infrastructure Network. The alliance will use electrically powered earthmoving machines in this project, making this an important step towards emission-free work in the infrastructure sector.
Energy transition
Due to emission-free construction, transport and use, existing energy grids simply cannot cope with the demand for electricity and are already running at full capacity. This will require major adjustments to and the expansion of both local grids and the main energy infrastructure to secure energy supplies in the future. The need for charging infrastructure is rising sharply, so much so that the charging requirements for 2030 are estimated at 1.7 million charging stations. What is more, the central government will require companies to only purchase electric company cars from 2025 onwards.
Heijmans is using pilots and innovations to develop solutions aimed at the affordability of energy, smart grids, sustainable power generation and the minimisation of CO2 emissions. Heijmans Property development and Heijmans Energy are working closely together to include energy as an integral part of an increasing number of area developments. Last year, we completed the acquisition of Dynniq Energy, which will be fully integrated in Heijmans Infra's energy domain in 2023. This acquisition strengthens our position in low, medium and high-voltage energy infrastructure, which looks to be a major growth sector due to planned investment volumes as a result of the energy transition. We are now even better positioned to respond to this expected growth.
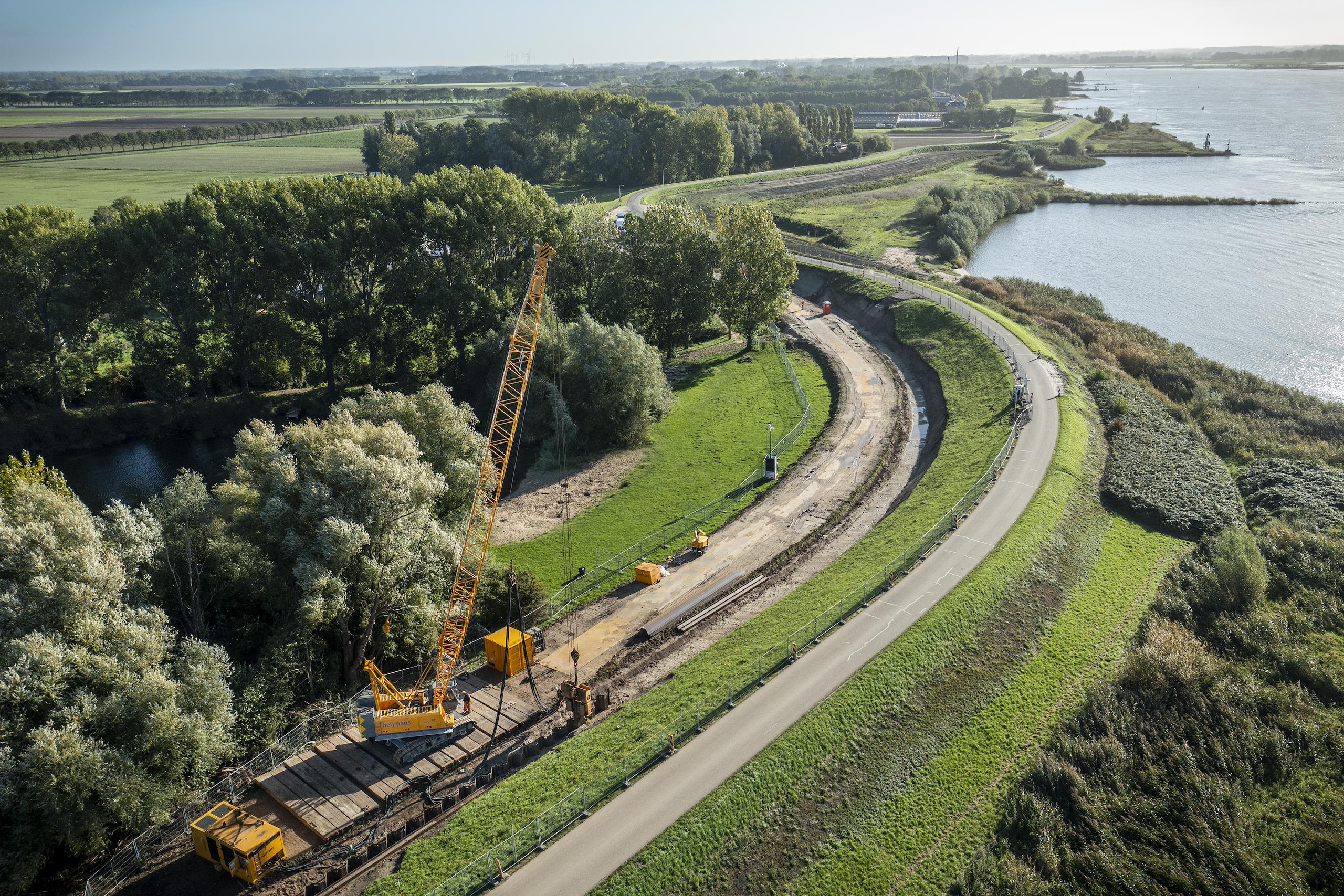
CO2 neutral
Heijmans’ ambition is to be CO2 neutral after 2023. This means that we will minimise our emissions and offset the remaining emissions. We have laid down our approach to this in an Energy Management Plan. And we have delegated implementation to four working groups, each responsible for one of the areas in which we are taking action: accommodation, vehicle fleet, building sites and equipment.
An increasing number of our clients are also demanding the use of sustainable equipment. For instance, the Dutch Ministry of Public Works and Waterways (Rijkswaterstaat), is aiming to be fully climate neutral and to work in a circular way by 2030 at the latest. Heijmans Infra is helping to fulfil this ambition by applying new technologies, reusing materials and using emission-free equipment. We are doing this in numerous projects, including the widening of the Apeldoorn-Twello stretch of the A1 motorway.
Energy from the IJssel
Heijmans is using thermal energy from surface water to sustainably heat homes in Zutphen's Noorderhaven district. A thermal energy storage system (Dutch: WKO) pumps hot and cold water from wells around 70 metres deep to power an apartment complex. To keep the amount of underground hot and cold energy in balance, Heijmans Energy developed a smart solution. TEO, the Thermal Energy from Surface Water system, is linked to the thermal energy storage system and restores the imbalance in the soil with water from the river IJssel in a sustainable way. The submersible pump hangs in the water and does its work quietly and invisibly. This system is a perfect fit with Heijmans Energy’s ambition to use smart solutions to combine the generation and distribution of energy with other tasks to accelerate the energy transition.
Nitrogen emissions
The nitrogen emissions issue remains a major concern. With insufficient latitude for nitrogen emissions available for permits, extra efforts are needed to prevent construction projects from being delayed or even halted completely. This has so far only affected a limited number of Heijmans projects. The issue is affecting residential building and the energy transition, but also infrastructure projects. Lack of latitude for nitrogen emissions is also putting pressure on new housing construction, which is serious given that we need to build 900,000 new homes in the period to 2030. This will require extra attention, otherwise the housing shortage will only continue to increase.
On the road to emission-free construction
Electrically powered construction machinery emits less nitrogen and CO2 and will be found at every building site in the future. In 2023, for instance, Heijmans will take 18 electric machines into service, from crawler cranes and wheel loaders to rollers. These are costly but necessary investments. For one, an increasing number of clients are demanding it, plus it helps create a healthy living environment. Heavy construction equipment, such as earthmoving and foundation machines, are major emitters on building sites. This is why Heijmans is investing heavily in the transition to electrification of this kind of equipment. The traditional combustion engine will be replaced by one or more electric motors and the required power will be generated using batteries. This ambition is part of Heijmans’ Energy Management Plan, aimed at reducing CO2 and other emissions and making the company’s work sustainable.
To emit less nitrogen in the future, we first need additional nitrogen latitude. On 2 November, the Council of State ruled that the generic construction exemption would no longer apply. Although this is obviously a setback, the ruling did not come as a complete surprise to Heijmans, and we were prepared for it. Projects that were under construction will continue and new housing projects are also still possible, provided nitrogen deposition during the construction phase remains within the legal limits. We can demonstrate this using Aerius calculations. Heijmans has already had Aerius calculations made for the construction phase for almost all the projects we are developing ourselves, so we will be able to keep any delays to a minimum.
Ageing infrastructure
Much of the Netherlands’ road network, bridges and viaducts date back to the 1960s and 1970s and are nearing the end of their lifespan. Moreover, many civil engineering structures such as bridges and viaducts are not designed for today’s intensive and heavy road traffic. Renovation is more sustainable and less expensive than demolishing and rebuilding these structures. This is why infrastructure maintenance and replacement market is expected to almost double in the coming decades. This will also create more demand for the management and operation of assets and the associated know-how and solutions.
In June, the government said that it was prioritising the improvement and maintenance of existing infrastructure. The Minister of Infrastructure and Water Management, Mark Harbers, wrote to the Lower House of Parliament, noting that there are not enough experts to carry out the mandatory nitrogen calculations and that choices will therefore have to be made with regards to which new infrastructure projects will be prioritised and which will have to wait. Maintaining the condition of our roads and infrastructure does require additional financial budgets and manpower. Larger infrastructure projects are also being affected by the cancellation of the construction exemption, despite the fact that the usage phase is the decisive factor here. We also see opportunities for the further reduction of nitrogen deposition during the construction phase by using electric equipment.
Pressure on the housing market
Demand for housing is a great as it has ever been. The biggest concern is the issue of affordability. It was already difficult for first-time buyers to buy a first home, but rising mortgage interest rates and energy costs have added to the problem of affordability and borrowing capacity for consumers. Nor has the fact that the focus in recent years has increasingly been on inner-city construction helped on the affordability front. Due to the high density of housing production, it is also proving difficult to achieve pre-sale rates of 70% in a declining market, which means construction is not started. In the second half of 2022, following the sudden rental market measures taken by the government, foreign institutional investors exited the Dutch market.
Also, as a result of the new rules, we are now seeing the inevitable reluctance of Dutch investors to invest in new housing construction. If we are to accelerate housing construction, one thing most definitely needed is more planning capacity. And not just for inner-city construction, as suburban housing construction will absolutely be necessary to realise the government’s new-build ambition in the coming years. However, due to relatively strong economic growth, we are also seeing that the concentration of housing construction and increasing mobility is putting urban liveability at risk. It is important to find smart solutions in a good balance between the various demands. For the medium term, Heijmans is confident about the housing market, as demand for housing will remain high in the coming years. New-build homes will remain attractive because they are more sustainable and energy efficient than existing buildings.
Heijmans is keen to help break the deadlock in the housing market. Among other things, we are seeing that more and more tenants, local residents and other stakeholders want to have a say in their living environment. This is why Heijmans actively seeks dialogue with citizens to create support for area development and real estate projects. We also help to increase planning capacity by identifying opportunities and taking the lead with our partners, as we did for Eemvalleistad near Almere/Zeewolde, for example. In addition, we are committed to the further standardisation and industrialisation to make production processes more efficient and by doing so make homes more affordable and sustainable and that they are of sufficiently high quality.
Industrial-scale construction
Conceptual housing construction has now more than proven itself in practice. The idea that conceptual building creates uniformity is long gone and we can certainly prove otherwise at several locations in the Netherlands. Our housing concepts offer enormous versatility in terms of types of home and a rich variety of facades, heights, roofs, floor plans and space for individual input. In addition to the increasingly sustainable and largely dismantlable concrete construction used in the Heijmans Huismerk homes, timber-frame construction looks very promising in term of more sustainable (circular) production for the coming years. From 2023, we will produce industrial-scale, conceptual, circular timber-frame homes in our own energy-neutral timber-frame factory in Heerenveen.
Amsterdam VERTICAL: high-level living and working
A new icon of Dutch Design is rising in Sloterdijk as part of the area development: VERTICAL. In this sustainable building, Heijmans is realising homes, commercial spaces and sub-facilities. A special feature of the stacked design is the abundance of greenery on the facades and roofs. The green residential landscape around VERTICAL will also help create a healthy living environment. Work on the project is currently still in progress, and will be completed in several phases. Thanks to sophisticated planning and coordination, everything is coming together perfectly.
Digitalisation
Digitalisation is playing a structural role in changing products and services. There are now millions of sensors running in public spaces, including cameras and other monitoring and measurement systems. On the basis of that collected data, we aim to make the management and maintenance of buildings and structures predictable, and use data-driven methods to influence the use of mobility, digital design and production processes, and ‘smart’ homes, buildings, grids and objects. A good example of this is our Beyond Eyes service, which uses a combination of smart sensors, data pooling and continuous monitoring to enable the smart use and management of buildings.
So, the domain of technology is changing and operating in this smart-sensor living environment (Smart City) currently requires very different know-how than before. This is why Heijmans has set up the 'Hive', a hub in which data science experts from across the organisation work together on various innovations. We do this in close cooperation with JADS, the Jheronimus Academy of Data Science in Den Bosch.
For Heijmans, digitalisation goes beyond the development of innovative products and services. It is also an important tool for the deployment of our people where they add the most value. When we can automate repetitive work and when data makes better planning possible, this gives us an opportunity to deploy our people more efficiently. And that is a significant advantage in the current and future labour market, which is why we continue to develop new digital tools. Furthermore, the digitalisation, automation and industrialisation of our processes is also helping us to improve safety.
Circularity
Circular thinking is gaining traction in our industry. The more we build in a circular fashion, the more we spare the climate and the environment. True circular thinking encompasses the entire life cycle of an object to be built, from design for reuse to life-extending maintenance and collecting and reusing the residual materials. However, switching to circular thinking requires change and a lot of effort. The evolution of material flows into cycles, for example, has major implications for the entire construction sector. Heijmans is contributing to this process of change by creating circular designs and building circular objects. We do this by looking for alternatives to materials, such as in the construction of houses using timber-frame construction methods, and also by working on new technologies. We can draw up a material passport for each project, which will make it easier to reuse materials in the future. To enable us to also reuse asphalt on a large scale and safely, last year AsfaltNu (a Heijmans and BAM joint venture) worked on a solution to reduce harmful emissions in the recycling process, including benzene, and the first results have been promising.
Rabobank gets a circular floor
In the centre of Utrecht stands the Glass Building, Rabobank's head office. Heijmans is revitalising this landmark building as part of a major architectural and installation technology renovation. Rabobank is aiming for future-proof living, housing and business, which is why the bank only works with companies that take into account the potential impact of their activities and try to avoid or limit this impact. Heijmans put Rabobank's sustainability ambitions into action by using electrically powered equipment, a more sustainably designed building site and by reusing materials. Nine circular materials were used in this renovation, plus Heijmans managed to reuse high-grade materials that were released during the renovation. This was achieved by working with Rabobank to challenge the chain of suppliers, demolition firms and waste processors on the sustainability front. For example, pure recycled gravel and sand were used in the concrete mix for a roof floor in this renovation project.
Pressure on availability and affordability
Last year saw significant rises in procurement prices in our industry and the availability of materials and labour is under pressure. Energy in particular, and the semi-finished products produced using that energy, are substantially more expensive than in the previous year. We too are facing price increases for materials and subcontractors, which means we cannot and will not take on larger works or works with a longer execution period without clear indexation agreements. Where this is not possible or the contractual frameworks are not reasonable, we choose not to take on the contract. So far, we have managed to pass on higher procurement costs in the sales prices of our products and services based on indexation agreements with external clients.